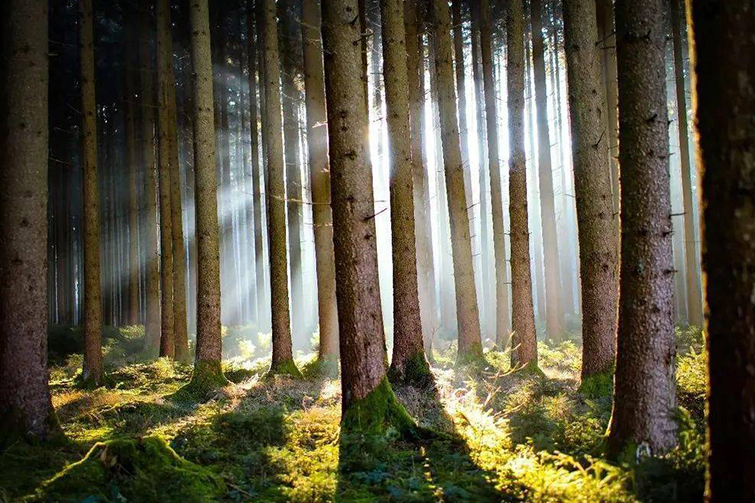
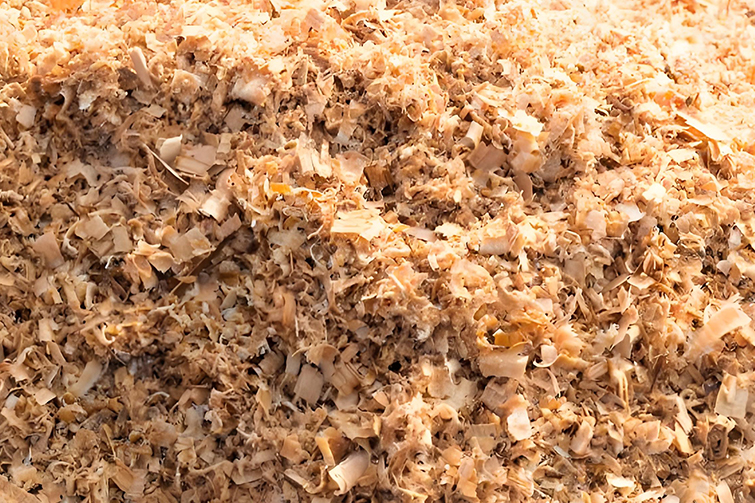
Types of Wood Briquette Machines: An Overview
Wood briquette machines are essential tools in the renewable energy industry, converting biomass materials into compact, solid fuel briquettes. These machines not only facilitate the recycling of waste materials but also contribute to sustainable energy solutions. Different types of wood briquette machines are available, each suited to specific materials, applications, and operational requirements. Here’s an in-depth look at the various types of wood briquette machines.
1. Screw Briquette Machines
2. Hydraulic Briquette Machines
3. Punching Briquette Machines
4. Roller Briquette Machines
5. Mechanical Stamping Briquette Machines
1. Screw Briquette Machines
Description
Screw briquette machines are the most popular type for creating wood briquettes. These machines use a screw mechanism to compress the raw material into briquettes.
Working Principle
- Material Feeding: Raw material is fed into the machine’s hopper.
- Screw Compression: A rotating screw propels the material through a heated die, compressing it into a dense, cylindrical briquette.
- Heating: The die is heated to reduce the friction and assist in binding the material.
- Forming: The compressed material is extruded through the die to form continuous briquettes, which are then cut to the desired length.
Advantages
- High Density: Produces high-density briquettes that burn efficiently.
- Versatility: Suitable for a wide range of raw materials, including sawdust, agricultural residues, and wood chips.
- Continuous Operation: Ideal for large-scale production with consistent output.
Applications
- Residential Heating: Commonly used for producing briquettes for home heating.
- Industrial Fuel: Used in industries for boiler fuel and energy generation.
Example Image
2. Hydraulic Briquette Machines
Description
Hydraulic briquette machines use hydraulic pressure to compress the raw material into briquettes. These machines are known for their ability to process high-moisture materials and produce high-quality briquettes.
Working Principle
- Material Feeding: The raw material is fed into a compression chamber.
- Hydraulic Compression: A hydraulic piston applies pressure, compressing the material into a briquette.
- Ejection: Once the desired pressure is reached, the briquette is ejected from the chamber.
Advantages
- High Pressure: Capable of applying very high pressure, resulting in extremely dense briquettes.
- Adjustable Density: Allows control over the density and size of the briquettes.
- Moisture Tolerance: Can handle materials with higher moisture content than other types.
Applications
- Metallurgy: Used for making briquettes from metallic powders.
- Agricultural Waste: Effective in converting agricultural waste into fuel briquettes.
Example Image
3. Punching Briquette Machines
Description
Punching briquette machines utilize a mechanical punching mechanism to compress the material into briquettes. These machines are often used for producing briquettes with a hole in the center, which helps improve combustion efficiency.
Working Principle
- Material Feeding: The raw material is fed into a pre-press chamber.
- Punching Action: A mechanical punch presses the material into a mold, forming a briquette with a central hole.
- Ejection: The formed briquette is pushed out of the mold.
Advantages
- Efficient Combustion: The central hole increases surface area, allowing for better air flow and efficient combustion.
- Durable Briquettes: Produces strong and durable briquettes suitable for various applications.
- Rapid Production: High-speed operation leads to faster production rates.
Applications
- Residential Heating: Commonly used for making heating briquettes for stoves and fireplaces.
- Industrial Processes: Suitable for industrial use where high-efficiency fuel is required.
Example Image
4. Roller Briquette Machines
Description
Roller briquette machines, also known as roller presses, use two counter-rotating rollers to compress the raw material into briquettes. This method is suitable for materials that are difficult to compact using other methods.
Working Principle
- Material Feeding: The raw material is fed between two rollers.
- Compression: As the rollers rotate, they compress the material into the cavities on their surfaces, forming briquettes.
- Ejection: The formed briquettes are released as the rollers continue to rotate.
Advantages
- Versatile Materials: Can process a wide variety of materials, including those with low or high moisture content.
- Consistent Size: Produces uniform briquettes with consistent size and shape.
- Continuous Production: Suitable for large-scale, continuous production operations.
Applications
- Coal Briquetting: Widely used for making coal briquettes.
- Metal Processing: Used in metallurgy for briquetting metal ores and concentrates.
Example Image
5. Mechanical Stamping Briquette Machines
Description
Mechanical stamping briquette machines are designed to produce dense, solid briquettes using a stamping mechanism. These machines are known for their high pressure and ability to produce briquettes with various shapes and sizes.
Working Principle
- Material Feeding: The raw material is fed into a hopper.
- Stamping Compression: A mechanical stamper applies pressure to compress the material into a mold, forming a briquette.
- Ejection: The formed briquette is ejected from the mold.
Advantages
- High Pressure: Generates high pressure, resulting in dense and durable briquettes.
- Shape Variety: Can produce briquettes in different shapes, such as round, square, or hexagonal.
- Efficient Production: Suitable for medium to large-scale production with high efficiency.
Applications
- Biomass Briquetting: Ideal for converting biomass materials like sawdust, straw, and rice husks into fuel briquettes.
- Agricultural Waste: Effective in processing agricultural residues into useful briquettes.
Example Image
Conclusion
Choosing the right type of wood briquette machine depends on several factors, including the type of raw material, production capacity, and the desired characteristics of the briquettes. Each machine type has its advantages and is best suited to specific applications. Understanding the unique features and capabilities of screw, hydraulic, punching, roller, and mechanical stamping briquette machines can help you make an informed decision for your briquetting needs.