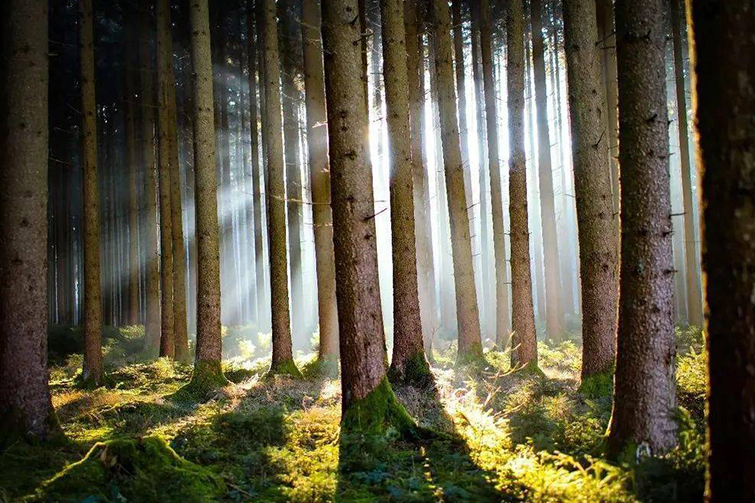
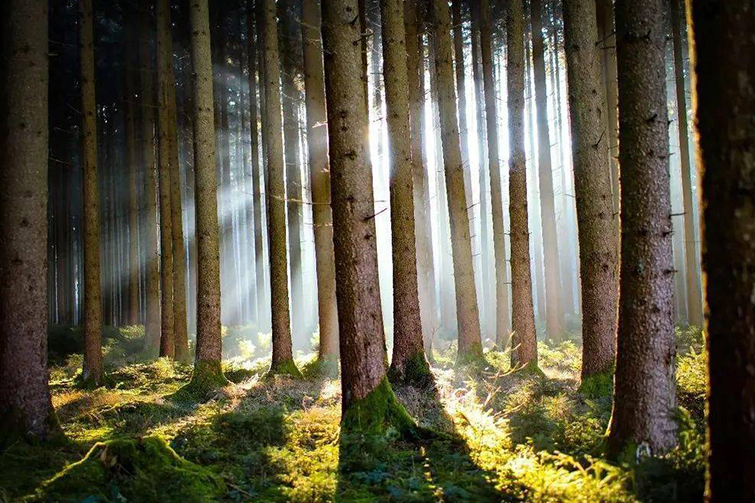
How to Build a Wood Pellet Factory: A Comprehensive Guide
Building a wood pellet factory involves several critical steps, from initial planning and site selection to equipment installation and production optimization. This guide will walk you through the entire process, ensuring you understand each stage involved in establishing a successful wood pellet manufacturing facility.
Steps to Build a Wood Pellet Factory
- Feasibility Study and Business Plan
- Site Selection and Preparation
- Securing Permits and Compliance
- Designing the Pellet Plant Layout
- Selecting and Purchasing Equipment
- Installation and Commissioning
- Raw Material Procurement
- Production Process Setup
- Quality Control and Testing
- Packaging, Storage, and Distribution
- Maintenance and Safety
1. Feasibility Study and Business Plan
Feasibility Study
- Market Analysis: Conduct thorough market research to understand demand, competition, and potential customer segments for wood pellets.
- Financial Projections: Estimate costs, potential revenue, and profitability. Include initial capital investment, operational expenses, and pricing strategies.
- Supply Chain Assessment: Evaluate the availability and cost of raw materials, logistics for transportation, and potential suppliers.
Business Plan
- Executive Summary: Outline your business objectives, mission, and vision.
- Operational Plan: Detail the production process, capacity, and schedule.
- Marketing Strategy: Plan how you will attract and retain customers.
- Financial Plan: Include detailed financial projections, funding requirements, and profitability analysis.
2. Site Selection and Preparation
Location Criteria
- Proximity to Raw Materials: Choose a location near sources of wood or other biomass to minimize transportation costs.
- Access to Utilities: Ensure the site has adequate access to electricity, water, and waste disposal facilities.
- Transportation Links: Select a site with good road, rail, or port access for transporting raw materials and finished products.
Site Preparation
- Land Acquisition: Secure the land required for the factory.
- Site Clearing and Grading: Prepare the site by clearing vegetation and leveling the ground.
- Infrastructure Development: Build necessary infrastructure, including roads, drainage, and utility connections.
3. Securing Permits and Compliance
Permits and Licenses
- Environmental Permits: Obtain permits related to air quality, waste management, and water usage.
- Building and Zoning Permits: Ensure compliance with local building codes and zoning regulations.
- Operational Licenses: Acquire necessary licenses for running a manufacturing facility, including health and safety certifications.
Compliance
- Environmental Regulations: Adhere to regulations concerning emissions, waste disposal, and noise levels.
- Safety Standards: Implement safety protocols to protect workers and equipment, and comply with Occupational Safety and Health Administration (OSHA) guidelines or local equivalents.
4. Designing the Pellet Plant Layout
Layout Planning
- Process Flow: Design the layout to facilitate efficient material flow from raw material intake to finished product packaging.
- Space Utilization: Optimize the use of space for equipment, storage, and operational areas.
- Accessibility: Ensure easy access for maintenance, material handling, and emergency exits.
Facility Design
- Building Specifications: Plan for the construction of buildings, including production halls, warehouses, and administrative offices.
- Environmental Controls: Incorporate ventilation, dust collection, and noise reduction measures into the facility design.
5. Selecting and Purchasing Equipment
Key Equipment
- Raw Material Handling: Conveyors, feeders, and hoppers for transporting and managing raw materials.
- Drying Systems: Rotary or flash dryers to reduce moisture content in raw materials.
- Grinding Mills: Hammer mills or chippers for reducing the size of raw materials.
- Pellet Mills: Flat die or ring die pellet mills to compress the raw material into pellets.
- Cooling Systems: Counterflow coolers to bring down the temperature of the freshly formed pellets.
- Screening Machines: Vibrating or rotary screens to remove fines and ensure uniform pellet size.
- Packaging Equipment: Bagging machines for packaging the pellets into bags or bulk containers.
Vendor Selection
- Reputable Suppliers: Choose suppliers with a proven track record and good customer support.
- Quality and Warranty: Ensure the equipment meets quality standards and comes with a comprehensive warranty.
- Service and Maintenance: Consider suppliers who offer after-sales service, maintenance, and spare parts.
6. Installation and Commissioning
Equipment Installation
- Professional Installation: Hire experienced technicians or engineers to install the equipment according to manufacturer specifications.
- Utility Connections: Ensure all equipment is properly connected to power, water, and waste disposal systems.
- Testing and Calibration: Test and calibrate each piece of equipment to ensure it operates correctly and efficiently.
Commissioning
- Trial Runs: Conduct trial runs to test the entire production line under operational conditions.
- Adjustments: Make necessary adjustments to optimize performance and address any issues.
- Training: Train your staff on operating procedures, safety protocols, and routine maintenance.
7. Raw Material Procurement
Sourcing Materials
- Wood and Biomass Suppliers: Establish contracts with reliable suppliers of raw materials like wood chips, sawdust, or agricultural residues.
- Quality Control: Ensure the raw materials meet quality standards and are free from contaminants.
Inventory Management
- Storage Facilities: Build adequate storage for raw materials to maintain a steady supply.
- Inventory Control: Implement inventory management systems to track raw material usage and reorder supplies efficiently.
8. Production Process Setup
Process Optimization
- Process Flow: Define and document the production process from raw material intake to finished pellet packaging.
- Efficiency Measures: Implement measures to optimize energy use, minimize waste, and improve productivity.
Automation and Control
- Automation Systems: Use automated systems for monitoring and controlling key aspects of the production process.
- Control Systems: Install control panels and software to manage and monitor equipment performance in real-time.
9. Quality Control and Testing
Quality Standards
- Pellet Quality: Set quality standards for pellet size, density, moisture content, and durability.
- Testing Procedures: Implement testing procedures to regularly assess pellet quality and ensure consistency.
Continuous Improvement
- Feedback Loops: Use feedback from quality tests to make continuous improvements in the production process.
- Employee Training: Train employees on quality control practices and encourage them to identify and report quality issues.
10. Packaging, Storage, and Distribution
Packaging
- Bagging and Sealing: Use automated bagging machines to package pellets into bags of various sizes.
- Labeling: Ensure bags are clearly labeled with product information, weight, and production date.
Storage
- Bulk Storage: Use silos or large containers for storing pellets in bulk.
- Bagged Storage: Store bagged pellets in pallets or racks in a dry, well-ventilated area.
Distribution
- Logistics Planning: Develop efficient distribution plans to deliver pellets to customers or retailers.
- Shipping: Arrange for transportation using trucks, rail, or ships, depending on the destination and volume.
11. Maintenance and Safety
Maintenance
- Routine Maintenance: Schedule regular maintenance for all equipment to prevent breakdowns and ensure optimal performance.
- Spare Parts Inventory: Keep an inventory of critical spare parts to minimize downtime in case of equipment failure.
Safety
- Safety Protocols: Implement safety protocols to protect workers from hazards associated with equipment and processes.
- Training and Drills: Conduct regular safety training and emergency drills for all employees.
- Fire Prevention: Install fire prevention systems and have fire extinguishers readily available.
Conclusion
Building a wood pellet factory involves careful planning, precise execution, and continuous management. From the initial feasibility study to the final product distribution, each step is crucial for establishing a successful and profitable operation. By following this comprehensive guide, you can set up a wood pellet factory that not only meets your business goals but also contributes to sustainable energy production.
If you need more detailed advice or assistance with specific aspects of setting up your wood pellet factory, feel free to reach out to industry experts or consultants who specialize in biomass pellet production.